Ферромарганец ФМн 78
ФЕРРОМАРГАНЕЦ ИСПОЛЬЗУЮТ ДЛЯ РАСКИСЛЕНИЯ СТАЛИ
Ферромарганец – сплав железа и марганца. В обшей структуре потребления марганца более 90% его используется в черной металлургии при выплавке стали в виде различных марганцевых ферросплавов.
Средний расход марганца в сталеплавильной промышленности различных стран мира зависит от нескольких факторов: марочного сортамента выплавляемых сталей, способа производства металла (кислородно-конвертерного, электропечного, мартеновского), научно-технического уровня технологических процессов и других. В странах СНГ удельный расход марганца высок и составляет от 7 до 9 кг на 1т стали.
Разнообразие марок стали и сплавов обусловливает необходимость получения марганца и марганцевых ферросплавов широкого сортамента.
Характеристика ферромарганца ФМн78(Б):
- Классификация - Ферромарганец;
- Дополнение - Высокоуглеродистый ферромарганец;
- Применение - В металлургической и литейной промышленности для легирования стали и её раскисления;
- Зарубежные аналоги - Нет данных.
Химический состав в % ферромарганца ФМн78(Б) ГОСТ 4755 - 91:
- C - до 7;
- Si - до 6;
- Mn - 75 - 82;
- S - до 0,02;
- P - до 0,7.
Механические свойства ферромарганца ФМн78(Б) - обозначения:
- σB - Предел кратковременной прочности, [МПа];
- σT - Предел пропорциональности (предел текучести для остаточной деформации), [МПа];
- δ5 - Относительное удлинение при разрыве, [ % ];
- ψ - Относительное сужение, [ % ];
- KCU - Ударная вязкость, [ кДж / м2];
- HB - Твердость по Бринеллю, [МПа].
Физические свойства ферромарганца ФМн78(Б) - обозначения:
- T - Температура, при которой получены данные свойства, [Град];
- E - Модуль упругости первого рода, [МПа];
- α - Коэффициент температурного (линейного) расширения (диапазон 20o - T ) , [1/Град];
- λ - Коэффициент теплопроводности (теплоемкость материала) , [Вт/(м·град)];
- ρ - Плотность материала , [кг/м3];
- C - Удельная теплоемкость материала (диапазон 20o - T ), [Дж/(кг·град)];
- R - Удельное электросопротивление, [Ом·м].
Наиболее распространенными марганцевыми ферросплавами являются:
- ферромарганец, включающий группы высокоуглеродистого и низкоуглеродистого ферромарганца с различными допустимыми пределами концентрации углерода, фосфора и других примесей;
- силикомарганец с широким интервалом содержания кремния примесями фосфора, углерода и др.;
- металлический марганец, включающий марки электролитического и электротермического способов производства;
- азотированные металлический марганец и силикомарганец.
Примерно такого же сортамента производятся марганцевые ферросплавы и в зарубежных странах.
Свойства марганца
Марганец – раскислитель. Взаимодействие марганца с жидким железом, содержащим кислород, приводит к раскислению металла по реакции: [Mn]Fe + [O]Fe = MnO. Раскислительная способность марганца ниже, чем у кремния, однако кремний не всегда создает условия для формирования желаемых оксидных включений. Введение силикомарганца обеспечивает более высокое качество стали.
Марганец - десульфуратор. С серой, растворенной в же¬лезе и расплавах Fe-С, марганец образует термодинамически прочный сульфид, который имеет малую растворимость в же¬лезе и его сплавах, поэтому марганец применяется в виде марганцевых концентратов в составе шихты для выплавки чу¬гуна с пониженным содержанием серы.
Марганец — легирующий элемент. В промышленных нелегированных сталях содержится 0,4-0,8 % Мn, в высоколегированных - до 12-16 % и даже до 25-30 %, в чугунах от 4 до 17 %. Поэтому в строительстве магистральных газопроводов разработаны и выплавляются в большом объеме высокопрочные низколегированные стали с марганцем, молибденом и другими элементами.
При увеличении содержания марганца от 1 до 1,8 % размер зерна феррита в марганец-молибденовых сталях с 0,09%. С уменьшается от 216 до 65 мкм, критическая тем¬пература хрупкости снижается с —58 до —118 °С. Общеизве¬стна износоустойчивая сталь 110Г13Л (1,1% С и 13% Мn), которая широко применяется для отливок деталей и изделий (железнодорожные крестовины, траки, зубья землеройных ма¬шин и др.), подвергающихся динамическим и истирающим на¬грузкам.
В аустенитных сталях марганец в сочетании с азо¬том заменяет дефицитный и дорогой никель. Разработано около 100 марок азот и марганецсодержащих сталей. Марганец применяют для получения сплавов на железной основе, например (75%Mn), легирования кремниево-алюмиевых сплавов и т.д.
Для легирования сталей необходимо применять низкофосфористые марганцевые ферросплавы. Выплавляют ферромарганец из марганцевых руд содержащих в основном пиролюзит MnO2 с содержанием 63% Mn. В качестве восстановителя применяют коксик размером 3-15 мм. Содержание золы в нем менее 12%, влаги менее 11%, фосфора менее 0.02%.
ГОСТ 4755 - 91 (ISO 5446 - 80)
ФЕРРОМАРГАНЕЦ
В первом отечественном учебнике по ферросплавному производству «Теория и практика выплавки ферросплавов в электропечах» (Григорович и др., 1934 г.) отмечалось:
- «По своему значению для производства стали ферромарганец занимает первое место в ряду ферросплавов. В качестве раскислителя он применяется в производстве всех сортов стали. Расход ферромарганца на раскисление определяется довольно точно цифрой в 0,9 % от веса стали в слитках. Марганец вводится также в сталь в качестве легирующей примеси: самостоятельно или совместно с другими элементами.
- В качестве же раскислителя стали марганец практически незаменим.
- Специальные стали, содержащие марганец, иногда уступают по качеству другим легированным сталям с содержанием хрома, никеля и т.д. Это имеет место для некоторых нержавеющих, жароупорных и других сталей. Но, учитывая дешевизну марганца и его относительно большое распространение по сравнению с другими легирующими элементами, надо подчеркнуть его значение в производстве специальной стали в качестве специальной добавки, придающей особо ценные свойства.
- Ферромарганец выплавляется до сих пор в большинстве стран в доменных печах. Объясняется это отсутствием дешёвой электрической энергии вблизи месторождений марганцовой руды. Только в некоторых странах условия достаточно благоприятны для развития электроплавки ФЕРРОМАРГАНЦА».
Из приведённой цитаты хорошо видно, что доменная плавка оставалась основным способом получения ферромарганца практически до середины XX в. Сама же технология производства ферромарганца в доменных печах была отработана уже к 1880 г. (как это отмечалось выше). Рассмотрим технологию производства ферромарганца в доменных печах в конце XIX в.
Первым необходимым условием для обеспечения приемлемого уровня содержания марганца в сплаве был подогрев воздушного дутья, подаваемого в печь. По мнению профессора Окермана, одного из основоположников «доменной науки», доменная печь, работающая на древесном угле, используя слабо нагретое дутьё, не может постоянно давать сплав, содержащий даже 50 % марганца. Для получения же сплава, содержащего до 80 % марганца, необходимо использовать в качестве топлива каменноугольный кокс, при этом температура дутья должна составлять 700 - 800 °С (достигается при помощи воздухонагревателей Каупера или Витвеля).
Наиболее удобным сырьём для выплавки ферромарганца были железисто-марганцевые руды с известковистой пустой породой, встречающаяся на восточном побережье Испании, в Италии и в некоторых других странах, с содержанием от 10 до 15 % железа и 25-30 % марганца. Там, где подобные руды отсутствовали, проплавляли смесь железных руд с настоящими марганцовыми рудами или соединениями марганца, полученными искусственно. Для получения сплавов с высоким 25 содержанием марганца использовали богатые марганцевые руды, содержащие ограниченное количество железа.
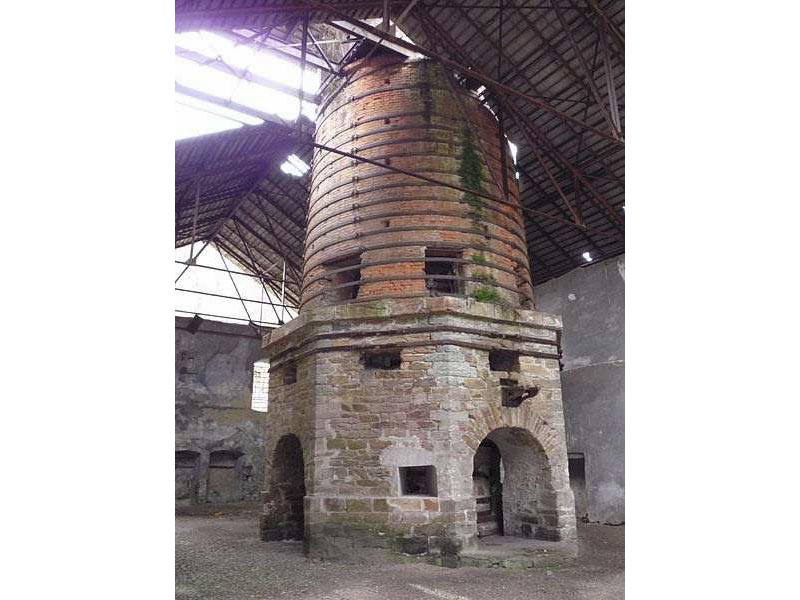
Шихта составлялась таким образом, чтобы получающиеся шлаки были основными (доля основных оксидов больше доли кислых), причём с ростом содержания марганца увеличивали и содержание основных оксидов в шлаке. Содержание марганца в сплаве влияло и на производственные показатели – помимо увеличения расхода топлива, сокращалась (довольно существенно) производительность печи. При этом вне зависимости от условий плавки и технологических ухищрений, не более 75-80 % марганца, поступающего с шихтой, переходило в сплав; остальная часть его переходила в шлак и частично улетучивалась с колошниковыми газами. Однако чем выше было содержание в исходной шихте марганца, тем меньшее относительное количество этого металла 26 уходило в шлак. Улёт марганца с колошниковыми газами был тем значительнее, чем выше температура в печи и чем богаче марганцем шихта.
Содержание в сплаве марганца, кремния и железа сильно зависело от свойств шихтовых материалов и технологических параметров процесса, что хорошо видно на примере работы двух европейских заводов.
На заводе в Тернуаре (Terre-noire, Франция) выплавка ферромарганца велась в обыкновенной доменной печи высотою 16 м и ёмкостью (полезным объёмом) около 100 м3 при температуре дутья 600-750 °С с использованием богатых марганцем руд, привозимых из Испании, с о-ва Сардиния, а также из департамента Соны и Луары.
При этом получаемый сплав фактически представлял собой ферросиликомарганец и имел следующий состав (образцы были выставлены в 1878 г. на выставке в Париже):
- Железо - 66.75, 71.50, 79.00, 85.50 %;
- Марганец - 20.50, 19.50, 13.00, 6.55 %;
- Кремний - 10.20, 7.45, 5.45, 5.55 %;
- Углерод - 2.65, 2.65, 2.30, 2.10 %;
- Фосфор - 0.185, 0.178, 0.145, 0.140 %.
Доменная печь в Крайне (современная Словения) высотой 17,2 м, работающая с повышенным давлением и с дутьём температурой около 600 °С, использовала шихту, составленную из местных шпатовых железняков (обожжённых) и из марганцевых руд, добываемых в окрестностях местечка Vigounsica. Также в шихту добавляли немного известкового флюса и оборотных шлаков.
При этом получались сплавы следующего состава:
- Железо - %;
- Марганец - %;
- Углерод - %;
- Кремний - %;
- Алюминий - %;
- Кальций - %;
- Сера - %;
- Фосфор - %.
Ферросилиций
Основными условиями получения кремнистого чугуна и ферросилиция были следующие: высокий нагрев дутья и расход горючего; кремнистые шлаки при работе на древесном угле и глиноземистые основные шлаки для хода на коксе; легковосстановимые небогатые руды с трудноплавкой пустой породой, свободный кремнезем которой равномерно распределен во всей массе оксидов железа.
В упомянутом выше учебнике «Теория и практика выплавки ферросплавов в электропечах» (1934 г.) отмечалось, что «при выплавке ферросилиция с 12 % кремния расход кокса устанавливается в 2,5-2,75 раза больше нормального. Отсюда видно, что расход горючего в доменной печи растёт не пропорционально увеличению концентрации кремния в сплаве, а в значительно большей степени. При достижении отношения железа к кремнию около 4:1 (кремния в сплаве около 20 %) дальнейшее увеличение расхода горючего не приводит к увеличению содержания кремния в сплаве, и поэтому более богатый ферросилиций получить в доменной печи нельзя, для этого требуется электропечь». Обычно в доменной печи выплавляли ферросилиций с 12-13 % кремния.
Выплавка ферросилиция в доменных печах производилась сравнительно редко, так как вследствие предельно горячего хода происходил быстрый износ футеровки печи. Поэтому, как правило, ферросилиций плавили в конце кампании перед окончательной выдувкой доменной печи для капитального ремонта.
Феррохром
Первые попытки получения феррохрома в доменных печах были сделаны ещё в середине XIX в. Несмотря на то, что восстановление оксидов хрома в доменной печи идёт достаточно полно, температурные условия не позволяют получить сплав с высоким содержанием хрома. Феррохром, выплавленный в доменной печи, содержит от 30 до 40 % хрома, сплав же с более высоким содержанием хрома настолько вязок, что не выходит из горна. Содержание углерода в феррохроме всегда было высокое – от 6 до 12 %.
По этим причинам к выплавке феррохрома прибегали лишь в особых условиях – например, эта технология эпизодически применялась на Урале в годы Великой Отечественной Войны.
Проблемы производства доменных ФЕРРОСПЛАВОВ
Использование доменных печей для выплавки кремний- и марганецсодержащих сплавов снимало проблему низкой производительности, характерную для тигельной и ваграночной плавки ферросплавов. Однако себестоимость сплавов оставалась очень высокой из-за особенностей технологии и высоких потерь марганца. Так как температура в рабочем пространстве агрегата должна была быть как можно более высокой расход топлива (кокса или древесного угля) достигал 3 т/т чугуна, а разгар горна был столь интенсивным, что, например, на Нижнетагильском заводе его делали сменным – выкатывающимся на специальной тележке по рельсам. Как уже отмечалось выше, из-за высокой температуры значительная часть марганца терялась с отходящими газами (при содержании в сплаве марганца более 80 % – до 20 % от его поступления в печь). Кроме того, содержание оксида марганца в шлаке иногда превышало 15 %, и потери марганца со шлаком достигали 12 % от общего содержания марганца в шихте. Таким образом, общие потери марганца в доменной печи достигали 27-32 %, а переход марганца в ферросплав составлял 68-73 % от общего количества его в шихте.
ФЕРРОМАРГАНЕЦ - преимущества получения в электропечах
Реакции восстановления марганца из руды и общий ход процесса получения ферромарганца в электропечи аналогичны процессам, протекающим при выплавке ферромарганца в доменной печи. Принципиальное отличие заключается в том, что при электроплавке топливо расходуется только на восстановление, и количество его на 1 т ферромарганца составляет примерно четверть расходуемого в доменной печи при одном и том же качестве.
Производство ФЕРРОМАРГАНЦА в электропечах:
- количество золы и вредных примесей, вносимых топливом, при электроплавке примерно вчетверо меньше, чем в доменной печи;
- количество шлака и потери с ним марганца при электроплавке существенно меньше;
- в электропечи можно применять восстановитель более низкого качества с большим содержанием золы, чем в доменной плавке.
В результате доменная печь уступает электропечи как по полноте извлечения марганца из руды, так и по качеству получаемого продукта. Поэтому с появлением в начале XX в. промышленных электропечей основной объём производства ферромарганца постепенно стал выплавляться с их помощью, хотя способ производства углеродистого ферромарганца в доменных печах используется и в наши дни.
Раскисление стали
Реализация технологии тигельной выплавки ферромарганца была впервые осуществлена на практике фабрикантом Пригером в Бонне в 1863 г. Следуя предложениям Бессемера, Пригер производил сплавы в тиглях, которые наполнялись смесью дроблёного чугуна, марганцевой руды, толчёного бутылочного стекла и угольного порошка, и подвергались продолжительному накаливанию в горне с коксом или в печи Сименса, до полного расплавления содержимого. При этом получались сплавы, содержавшие до 60 % (обычно около 25 %) марганца, а также некоторое количество кремния и углерода. Способом Бессемера-Пригера пользовались на многих сталеплавильных заводах, однако вскоре от него отказались из-за высокой стоимости и существенных потерь марганца. Схожий способ предложил Вильямс, в качестве восстановителя использовались углеродсодержащие жидкости – нефть, смола, дёготь и т.п.
Одновременно развивались и другие способы. В 1862 г. Бессемер узнал, что большое количество марганца образовывалось на химическом заводе Тэнннатов в Шотландии в составе отходов производства хлора и белильной извести. Посетив предприятие, Бессемер изложил свою идею тамошнему химику Гендерсону и договорился с ним, что тот разработает соответствующий процесс. В 1863 г. Гендерсон взял патент на производство «ферромангана» (в России его называли обычно железо-марганцем) с содержанием марганца 20-25 %. В ходе дальнейшего развития процесса содержание марганца в сплаве было доведено до 35 %. Гендерсон производил ферроманган без использования тигля, непосредственно в регенеративных печах Сименса с углеродистой футеровкой.
Вообще содержание марганца в сплаве, независимо от способа производства, зависело от температуры, при которой шёл процесс – чем выше она была, тем больше марганца восстанавливалось. Кроме того следовало ограничивать поступление кремния, который способствовал переходу марганца в шлак. В 1868 г. на заводе в Тернуаре (Франция) в доменных печах производили ферроманган с содержанием марганца 80 %.
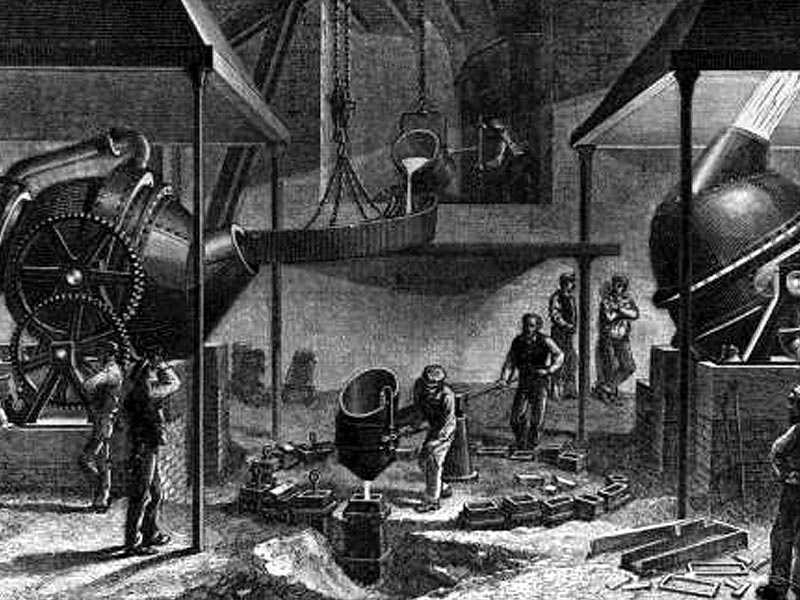
В итоге в последней четверти XIX в. основным способом получения ферромарганца стала доменная плавка, также использовались небольшие шахтные печи, по конструкции схожие с доменными. Высокий уровень отработки технологии позволил уже в 1875 г. получать в доменных печах, дутьё которых нагревалось с помощью воздухонагревателя Каупера, сплав с 62-70 % марганца. К началу XX в. удалось достичь содержания марганца 90-94 % при 5-6 % углерода.
Таким образом, марганец, являясь с одной стороны относительно легковосстановимым металлом, который можно эффективно получать в доменной печи, а с другой стороны – элементом, связывающим серу и кислород в стали, стал первым «большим» ферросплавом, масштабно производимым для нужд чёрной металлургии.Также в доменных печах в конце XIX в. выплавляли ферросилиций и ферросиликомарганец (кремнистый железо-марганец или «ферро-манган-силициум» по терминологии того времени) с содержанием кремния до 10 % и марганца – до 30 % (хотя нередки были случаи получения сплава с содержанием этих элементов на уровне нескольких процентов). Существовали другие способы получения ферросилиция – например, восстановлением кремния из его соединений в тигле металлическим натрием (металлотермия), однако они требовали больших затрат и в промышленности не применялись.
Вообще же на первом этапе развития ферросплавного производства (1825-1870 гг.) основным способом получения легирующих добавок была тигельная плавка, однако таким образом можно было получить материал для производства среднего и мелкого масштаба.
Металлургия электропечных ФЕРРОСПЛАВОВ т легированной стали начала XX в.
К 1920 г. во всех промышленно развитых странах мира практически все ферросплавы за исключением ФЕРРОМАРГАНЦА производились в электропечах. Масштабы их производства увеличивались быстрыми темпами, поскольку непрерывно росла потребность в легированных сталях специального назначения. Ниже приводятся данные, иллюстрирующие этот процесс для США (вплоть до Великой депрессии 1930 г.) и Швеции, которая располагала значительными ресурсами электроэнергии и много ферросплавов производила на экспорт. Впрочем, аналогичный рост производства ферросплавов наблюдался и в других западноевропейских странах.
Производство ферросилиция
Наряду с ферромарганцем ферросилиций являлся наиболее употребительным ферросплавом в производстве всех сортов стали (кроме «кипящей» мартеновской стали). Кроме применения в качестве сильного раскислителя ферросилиций широко использовался для получения специальных сталей с высоким содержанием кремния. На первых порах ферросилиций выплавлялся преимущественно в печах, построенных для выплавки карбида кальция, на ряде мелких заводов Франции, Австрии и Швейцарии. В 1903 г. был основан синдикат по производству всех сортов ферросилиция под руководством Campagnie Generate d'Electrochimie, охватывающий Германию, Францию и Австрию. Затем производство возникло в США, Швеции и Норвегии. В 1920-30 гг. лидерами в производстве ферросилиция были США, Канада, Скандинавские страны, Франция, Италия.
Ферросилиций применялся в производстве стали как бедный, с содержанием 12-13 % кремния, так и богатый, содержащий от 45 до 90 %. Согласно принятой в СССР в 1931 г. классификации (по аналогии с европейскими стандартами) ферросилиций производился четырех сортов, отличающихся по содержанию кремния.
13 %-ный ферросилиций производился в доменных печах и использовался в мартеновской плавке для раскисления металла. Остальные сорта выплавлялись в электропечах. Большое количество высокопроцентного ферросилиция расходовалось на получение ферросплавов (ферромарганца, хрома, ванадия) с низким содержанием углерода путем силикотермической реакции, например: 2Cr2O3 + 3Si = 2Cr2 + 3SiO3 + Q.
Эта реакция идет с выделением тепла, как и большинство других силикотермических реакций, поэтому методы силикотермии имели особое значение в металлургии ферросплавов.
Производство феррохрома
Промышленное производство феррохрома в электропечах было начато Полем Эру в 1899 г. Технология получила быстрое распространение и после Первой Мировой войны весь феррохром стал выплавляться в электрических печах. Использовались высокосортные хромиты и восстановители: кокс, антрацит и древесный уголь. Уже в это время ясно обозначилась основная проблема процесса – склонность восстановленного хрома к насыщению углеродом за счёт образования карбидов. Необходимость использования высокосортных хромитов в процессе получения феррохрома и высокая кратность шлака заставили специалистов искать более совершенные и экономичные методы рафинирования.
Стоит отметить, что электроплавка быстро заняла лидирующие позиции в производстве ферросплавов, однако отнюдь не вытеснила полностью другие способы извлечения легирующих элементов из руд (кроме, разве что, тигельного). Если давно «забытый» способ производства ферросплавов оказывался, вдруг, экономически эффективен в сложившихся условиях, его в ряде случаев брали на вооружение.
Так, уходящий корнями в глубокую древность способ производства природнолегированного металла использовался, к примеру, когда во второй половине конце XIX столетия в России усиленными темпами начали строить железные дороги. Есть сведения, что рельсы уральского КатавИвановского завода обладали настолько высоким качеством, что неизвестно ни одного случая рекламаций на них. Установлено, что катав-ивановский чугун выплавлялся из чистых по сере и фосфору высокожелезистых руд, к которым добавлялась бедная по железу местная руда, содержащая хром и марганец. Полученный из неё природно-легированный чугун продували воздухом в бессемеровском конвертере, получая природно-легированную хромомарганцовистую рельсовую сталь.
Ферросплавное производство в России XIX в.
Отечественная практика производства ферросплавов в XIX в. в основном соответствовала мировым тенденциям. Однако имелись и существенные отличия: даже на лучшем предприятии России того времени – Нижне-Тагильском заводе – выплавка богатого ферромарганца (50-60 %) в доменных печах непосредственно из руд оказывалась невозможной. Такой ферромарганец получали в результате доменной плавки с использованием чугуна и оборотного шлака. Путём обычной доменной плавки из марганцевой руды Лебяжьей горы получали ферромарганец с содержанием марганца 40 %, при этом при малейшем ухудшении хода плавки значительно увеличивались потери марганца в шлак (содержание оксида марганца MnO в шлаке составляло от 30 до 60 %). Расход древесного угля составлял 4,25-4,5 т/т сплава.
Через 6-7 дней горн сильно «разгорался» (т.е. происходил сильный износ огнеупоров горна с увеличением его размеров) и содержание марганца в сплаве снижалось. Тогда переходили на выплавку кремнистого чугуна (3-7 % кремния), который затем перерабатывали на сталь в бессемеровском конвертере. Через 1-2 дня из-за тугоплавких настылей горн сужался и можно было вновь выплавлять ферромарганец. Как уже упоминалось выше, горн делался съёмным и менялся каждые 6 недель.
Для повышения содержания марганца применяли двустадийную схему производства. По первому варианту смесь марганцевой руды и древесного угля с добавками железной руды и извести помещали в ящиках на 10 дней в цементационную печь, где и происходило первичное восстановление. Затем полученный спёк переплавляли в доменной печи. Однако такой способ оказался чрезвычайно дорого и от него вскоре отказались. Второй же вариант предполагал использование в качестве источника марганца оборотного шлака, который получался в ходе обычной плавки на ферромарганец и содержал, как уже говорилось, до 60 % MnO.
Для обезуглероживания ферромарганца (если была такая необходимость) его помещали в смеси с магнитным железняком в ящиках в цементационную печь. Процесс продолжался в течение 10 дней, по истечении которых содержание углерода не превышало 0,3 %.
С 1878 г. Нижне-Тагильский завод стал (в той же самой печи) готовить ферросиликомарганец (ферро-силициум-манган). Для получения этого продукта плавка велась сначала на кремнистый чугун, а затем, когда печь хорошо разогреется, начинало засыпать марганцевую руду и оборотный шлак. Получаемый сплав содержал от 40 до 45 % марганца и от 3 до 7 % кремния. В этой же печи производили ферросилиций, используемый для раскисления мартеновской стали и содержащий от 6 до 9 % кремния.
Тигельное производство ферромарганца
Сплавы, содержащие трудновосстановимые элементы – хром, титан, вольфрам, никель – первоначально получали только тигельным способом. Согласно «Энциклопедии промышленных знаний» (1901 г.), «выплавка феррохрома из руды производится очень просто». Для этого вручную, с помощи лопаты, готовили смесь руды, 12-15 % древесного угля, 6-7 % истёртой в порошок смолы, около 5 % битого стекла и 10-12 % кварцевого песка. Полученную массу помещали в графитовые или глиняные тигли, оставляя место для тонкого слоя мелкобитого стекла и более грубых кусков древесного угля. После этого тигель закрывался крышкой, которую плотно примазывали к краям глиной, оставляя в ней лишь небольшое отверстие для выхода газов.
Затем тигли помещались в регенеративную печь, как правило, конструкции Сименса (прообраз мартеновской печи), либо специально сконструированную для производства ферросплавов, например, конструкции Борхерса. Выплавленный таким образом феррохром получался в виде слитка («штыка») по форме соответствующего внутреннему профилю тигля. Аналогичным образом получали ферровольфрам.
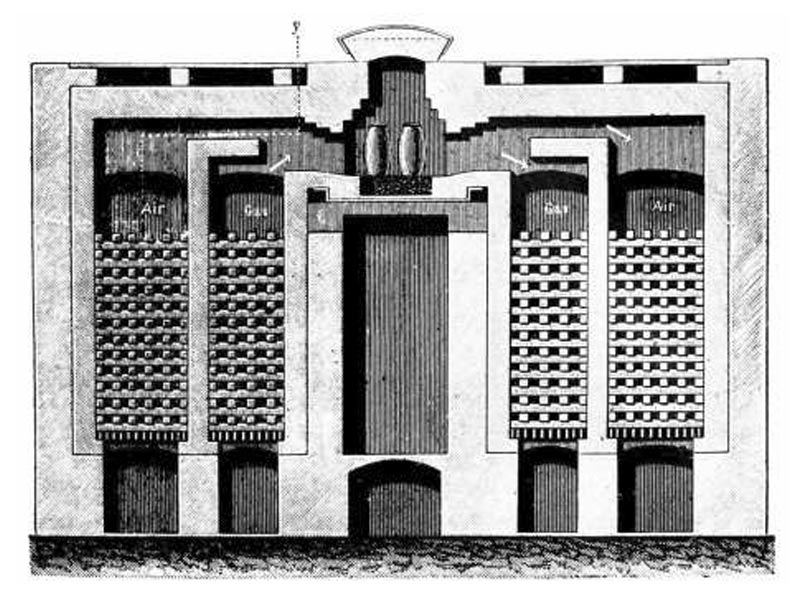
Крупномасштабное производство феррохрома и хромистой стали было организовано в Германии: в Ганновере Бирманом в 1873 г. и на заводе Хальцера в1875 г. Бруштлейном. В 1886 г. Гадфильд опубликовал подробные исследования о свойствах и способах производства железохромо-углеродистых сплавов.
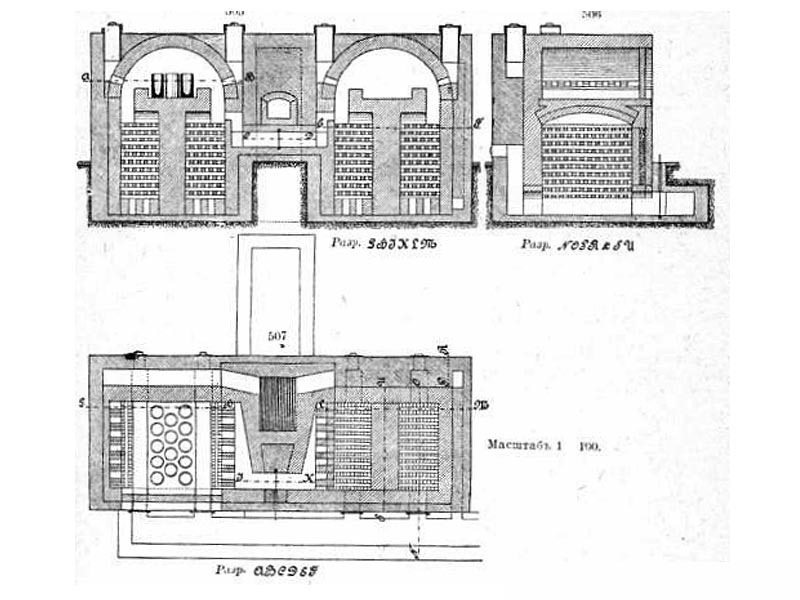
Существовали более сложные схемы получения металлов, руды которых содержали большое количество примесей, либо содержание которых в рудах было низким. В этом случае сначала тем или иным способом получали промежуточный продукт с достаточно высоким содержанием производимого металла, а затем уже в тигле производили рафинирование полученного полупродукта. Таким образом производили, например, никель – различными способами, зависящими от типа используемой руды, получали черновой никель, который затем переплавляли в тиглях.
Применялись и другие способы получения, как ферросплавов, так и чистых металлов. Например, в 1854 г. удалось получить чистый металлический хром электролизом водных растворов хлорида хрома, аналогичным способом получали высокочистый никель. Однако в основном это было лабораторное либо мелкомасштабное производство – экономически целесообразно было производить ферросплавы в тиглях.
Главными проблемами тигельного производства были высокие затраты и низкая производительность. Поэтому уже в 1880-х гг. марганец- и кремнийсодержащие ферросплавы, которые применялись, в первую очередь, для раскисления стали, производили практически исключительно в доменных печах.
В начале XX в. тигельный способ производства применялся для получения мало- и безуглеродистых ферросплавов, прежде всего – малоуглеродистого ферромарганца. Силикотермический метод получения малоуглеродистого ферромарганца запатентовали в 1893 г. Уильям-Фауст Грин и Уильям Генри Уэль. Однако из-за высокой цены малоуглеродистого ферромарганца спрос на него был чрезвычайно мал, и потому силикотермический метод производства малоуглеродистого ферромарганца долгое время не находил промышленного применения. Он был востребован лишь после Первой Мировой войны.
В первой половине XX в. для производства малоуглеродистого ФЕРРОМАРГАНЦА (и других безуглеродистых ферросплавов) использовались алюминотермический и силикотермический методы.
Алюминотермический метод применяется, главным образом, для получения металлического марганца. В подогретый магнезитовый тигель загружали хорошо перемешенную смесь порошкообразных оксидов марганца и металлического алюминия Процесс инициировали с помощью специальной зажигательной смеси в отдельном участке тигля. При повышении температуры оксиды марганца начинали реагировать с алюминием. За счет теплоты этой экзотермической реакции активно нагревались соседние участки в тигле, и там точно так же происходило восстановление марганца. Тепловой эффект горения алюминия столь велик, что в очень короткое время все содержимое тигля нагревалось до высокой температуры без подвода тепла извне, что обеспечивало практически полное восстановление оксидов марганца. В учебнике «Теория и практика выплавки ферросплавов в электропечах» (1934 г.) отмечалось: «метод этот не требует сколько-нибудь заметных капитальных затрат: оборудование состоит из одного лишь тигля, не нагреваемого ни током, ни газом, ни другим источником тепла».
Для получения малоуглеродистого ФЕРРОМАРГАНЦА в промышленном масштабе пользовались классическими силикотермическими методами Джина и Беккерта. По способу Джина процесс получения малоуглеродистого ферромарганца осуществлялся в две стадии: сначала получение силикомарганца, содержащего незначительное количество углерода, затем рафинировка силикомарганца от кремния марганцовой рудой. По способу Беккерта оксиды марганца восстанавливались богатым ферросилицием. Сложный метод Джина, при котором сначала кремний восстанавливали, чтобы получить силикомарганец с содержанием около 30 % кремния, а затем окисляли и переводили в шлак, имел целью достижение минимально возможного содержания в сплаве углерода.
Производство ферросплавов в вагранках
Распространенным способом получения ферросплавов тугоплавких металлов, прежде всего феррохрома и ферровольфрама, в конце XIX – начале XX в. была плавка в вагранке – небольшой шахтной печи, схожей по конструкции с доменной. Данная технология просуществовала до середины XX в., и широко применялась в случаях ограниченности ресурсов электроэнергии. В частности, ваграночная выплавка феррохрома и ферровольфрама применялась в СССР и имела характерные технологические особенности.
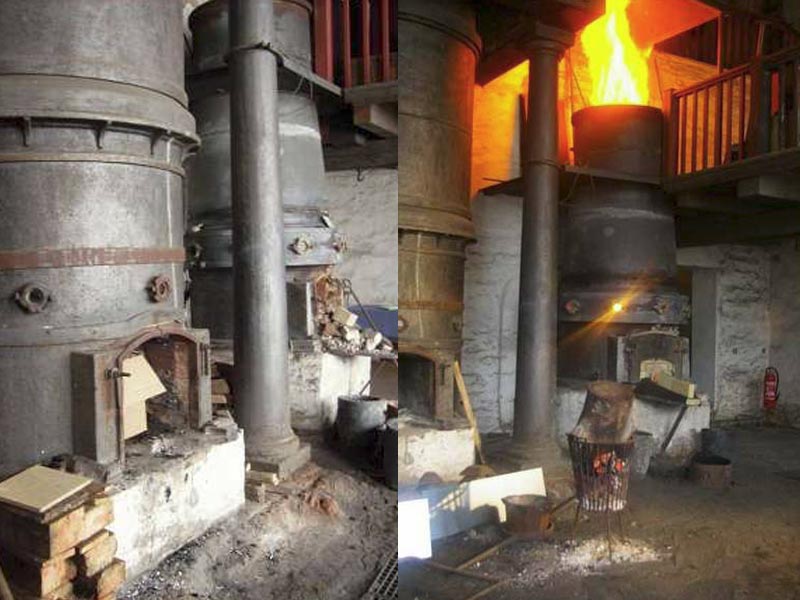
Выплавка феррохрома и ферровольфрама в вагранках велась «на козла» – т.е. полученный сплав ввиду своей тугоплавкости не вытекал в жидком виде из печи, а оставался внутри неё в виде слитка – «козла». Вагранки устраивались с откидным дном для удобства извлечения слитка.
Плавку феррохрома вели на брикетах, состоящих из кокса, хромита, соды и смолы. Воздушное дутьё предварительно нагревали до 400-500 °С. Плавку вели до тех пор, пока «козёл» не затянет фурм для подачи воздуха, которые устраивались в три ряда по высоте вагранки (на фото представлена вагранка с одним рядом фурм).
За одну плавку получали около 3 т феррохрома. Длительность кампании, включая время на охлаждение и футеровку вагранки, составляло около 7 дней. Расход кокса достигал 5-6 т на тонну феррохрома.
Плавка ферровольфрама осуществлялась также «на козла», получали сплав с содержанием вольфрама 78-84 %. Содержание углерода обычно составляло 0,1-0,7 %, столько же марганца и кремния; доля меди, олова и серы – менее 0,1 % для каждого компонента.
Реакция восстановления вольфрама углеродом из минералов (вольфрамита, шеелита) при этом шла очень быстро, поскольку конечные продукты процесса энергично уходят из системы: образующийся СО – удаляется с отходящими газами, а частицы ферровольфрама, обладающие громадным удельным весом по сравнению со шлаком (удельные веса 16,0 и 3,0), легко осаждаются на подину и, наплавляясь, образуют там «козёл». При этом верхний слой «козла» на подине вагранки представляет собой металлическое «болото», растворяющее вольфрам и железо. При нормально идущем процессе перегретые, подвижные частицы шлака, запутавшиеся в «козле», легко всплывают, и сплав получается монолитным. Поэтому после окончания плавки осуществляли выдержку для освобождения «козла» от включений.
При чрезмерно горячем процессе происходило восстановление значительного количества нежелательных примесей, в частности кремния и углерода. По этим причинам выплавка из руды ферровольфрама с содержанием больше чем 84 % вольфрама не осуществлялась. Сплав был настолько тугоплавок, что его трудно было получить монолитным (без включений) или чистым по кремнию.
Получавшийся шлак с высоким содержанием WО3 возвращался в процесс на переплав.